Research, Development, Innovation. Continuous improvements in design, materials, purpose, and process will lead to a better final product and drive growth for a business. As Ralph Waldo Emerson once put it "Build a better mousetrap, and the world will beat a path to your door". Could jet printing in the PCB production process be a “better mousetrap”?
Stencil printing has been a main-stay process in the SMT industry for years. In a nutshell, the PCB stencil is used to deposit solder paste on particular areas of a printed circuit board (PCB) so that components can be placed, aligned and affixed. The goal of stencil printing is to deposit the correct amount of solder paste so that the resulting solder joint between component and pad provides an electrical connection and mechanical strength.
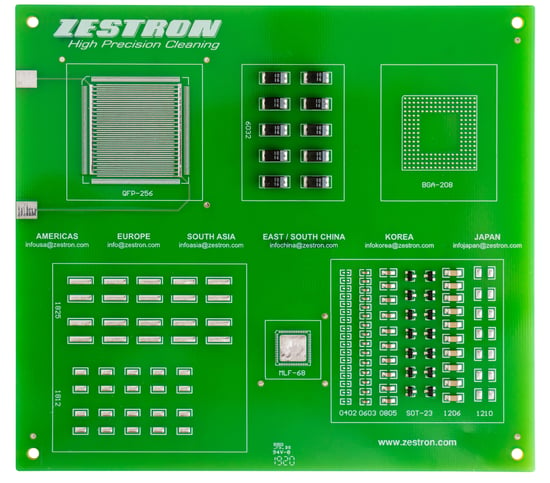
However, stencil printing has become more difficult in recent years due to the complexity of modern PCB designs. Today, you’ll encounter printed circuit boards that are more densely populated with smaller components surrounding larger components. There is only so much real-estate available, and PCB designers are making every little bit count. This complexity has stretched the limits of the stencil printing process.
Enter Jet printing. Jet printing accurately deposits precise amounts of solder for specific components with precise control of the throughput. It streamlines production and allows for easy change over to new board designs using Gerber and CAD software. With jet printing, there is no need for stencil or wipe materials which can reduce process costs. Combine these points, and it becomes easier to understand why jet printing is an attractive option for many.
At this point, you might say “that’s great! We’ve made a better mousetrap! Cheers to progress!” Well, with most advancements come challenges. Cleaning soldered fluxes from jet-printed solder pastes can be a challenge. This is due to the type 5 and type 6 solder pastes that are typically used. These solder pastes feature finer solder powder with higher flux activity levels. Left uncleaned, this can lead to more exposure to the typical causes of board failure like electrochemical migration. Additionally, cleaning under low standoff components (which is already challenging with stencil-printed PCBs) becomes even more of a challenge. Due to the lower powder size, it has been observed that the standoff height (space between the bottom of the component and the PCB surface) is even lower. This increases the difficulty in cleaning flux residues from under these low standoff components.
Solutions to this challenge do exist. To successfully clean flux residues associated with jet printed solder paste, choosing the right combination of cleaning agent and cleaning machinery will help to ensure the reliability of jet printed boards. Evidence suggests that a process optimized to clean flux residues of traditional screen-printing pastes may not produce the same results if an equivalent jettable solder paste is used instead.
So, is it a better mousetrap? Time and decreases in soldering errors will tell.
Effectively cleaning soldered jet printed solder paste residues remains a focus for both process users and those companies hard at work developing the cleaning agents. When it comes to cleaning jet printed solder paste residues, we’d suggest you get insight and help from the experts at machine manufacturers and PCB cleaning companies. Aligning yourself with the right partners will make all the difference.