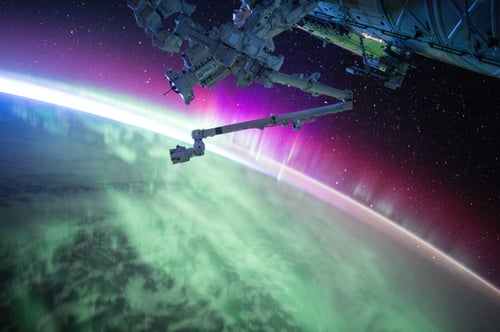
Imagine a space shuttle. A place where it’s important – perhaps more important than any other place a human being can be – to keep the inside and the outside environments separate. The airlock is the conduit between the inside and outside and makes this separation possible. While the American, Russian, and Chinese space agencies all design airlocks a little differently, they all operate on the same basic principle.
Let’s bring this metaphor down to earth and relate it to a printed circuit. The copper pathways through the PCB are how electricity gets around; like the astronauts moving inside the shuttle. The pathways terminate (one might even say “finish”) at the surface of the board, but direct exposure to the environment outside causes oxidation and deterioration of the copper, rendering the board useless. In our space shuttle it would be like trying to go on a spacewalk but the airlock is deteriorated and damaged. It’s…bad.
On PCBs it becomes necessary to apply a protective and conductive surface finish to the copper terminals. In the past, PCB surfaces were treated with Hot Air Solder Leveling (HASL), a process in which the board is dipped into liquid solder and excess solder is cleaned off with an air knife.
As boards and components become more complex and stand-off heights shrink, thinner and more precise surface finishes are needed. Newer finishes like Immersion Tin (ImSn), Immersion Silver (ImAg), and Electroless Nickel Immersion Gold (ENIG) have become more widely used alternatives. These processes use molecular bonding to create a protective layer on the copper terminals where components will ultimately be soldered. Like the international differences in airlock designs, these surface finish processes are slightly different approaches to accomplish the same goal.
Now let’s imagine NASA has spent the time and effort to install the airlock, and when the cleaning crew comes through, they damage the airlock seal with a power washer. This situation, again, is bad. The older HASL surface finishes could be cleaned with harsh alkaline surfactants or solvent-based cleaners without affecting the solder. The newer finishes use metals that are sensitive and can be chemically damaged during the PCB cleaning process by those traditional cleaners. This renders them less effective.
To deal with these sensitive metals, the chemical cleaning industry has engineered new formulations, including dynamic surfactants, and micro or single phase cleaning products that are either pH neutral or alkaline and contain inhibition packages to protect certain materials during the cleaning process.
While there may not be as much variety in surface finishes as there are ways to build a space shuttle airlock, there are still a few variables to consider including the appropriate cleaning process. As the technologies behind surface finishes continue to evolve, cleaning chemistry will also evolve and continue to be engineered with material compatibility in mind.
Learn more about pcb surface finishes with the video below.