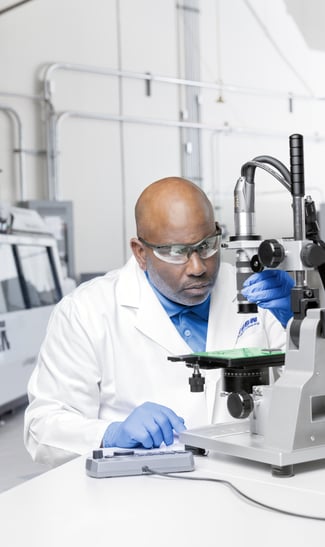
In the world of high-reliability applications, knowing how clean your cleaned PCBs are matters quite a bit. Impurities left on a board’s surface or underneath components may increase the risk of field failures. Risk tolerance varies based on what you’re producing, but risk exposure should be a known quantity. Depending on the class of assembly you’re assembling (I, II, or III), there are several tools and methods that can be used to assess the effectiveness of a PCBA cleaning process. Let’s take a look at a few of the most common.
Visual inspection is the easiest and most straightforward assessment. This is a quick and simple method of assessing surface cleanliness under 30-50X magnification. If you’re running a “clean” process and flux residues are present enough to be seen, it may adversely affect the board’s reliability. Additionally, if you’re currently using a “no-clean” process, you may find that flux residues are still present.
Ionic contamination testing offers an examination of overall cleanliness. Ionic contamination testing (a.k.a. ROSE Test) is an extractive analysis technique that enables the quantitative measurement of ionic contamination on PCBs. This is a valuable process control tool to assess if a PCB conforms to the user’s cleanliness specification. Ionic contamination testing can provide proof of cleanliness after soldering, can be used to define initial cleanliness standards, and act as a continuous quality control tool.
The new IPC standards indicate that the ROSE test can be used as a process verification tool but cannot solely be used as a process qualification tool. Other tests should be completed to create enough objective evidence. This is where tests such as Ion Chromatography, SIR, and FTIR come into consideration.
For an even more precise answer to the question “how clean is clean?”, ion chromatography testing can be used. This high-resolution analytical method precisely determines the ions present (anions, cations, and weak organic acids) on your assemblies. Ion Chromatography testing is useful as a predictive assessment of potential failures such as electrochemical migration or leakage current. It can be used in surface qualification after cleaning or before subsequent coating or bonding processes.
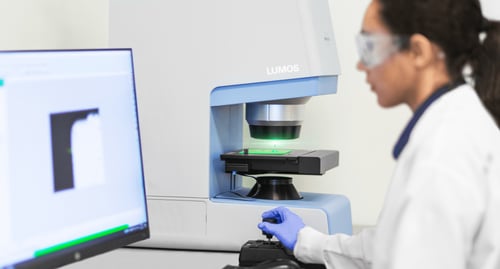
FTIR (Fourier Transform Infrared Spectroscopy) testing maps the locations and identifies organic contaminants on the board surface. FTIR testing can be used as a qualitative and (semi-) quantitative analysis of organic residues on surfaces, and to identify chemical structures of contaminants, residues, films, particles, etc.
Lastly, SIR (Surface Insulation Resistance) is a quantitative test method used to characterize the PCB manufacturing process residues and their impact on reliability. This is ideal when the goal is to understand the impact of flux residues on the electrical reliability of a device, and the user requires an effective predictor of long-term failure mechanisms and service life reliability.
Today’s SMT electronics cleanliness assessment tools afford more variety and depth of information than ever. Understanding "How clean is clean" includes knowing which analytical testing to use and that depends on your risk tolerance and the contaminants you’re trying to identify.
For more information and to take part in an in-depth discussion on this topic, please join ZESTRON Academy on July 26th at 11:00am EDT for a FREE webinar entitled Surface Cleanliness Assessment.